Thermoforming: A Process for Packaging and More
What is Thermoforming?
Thermoforming is a process of heating thermoplastic sheet and placing it over a mold until cooled. The thickness of the material determines whether the manufacturing process uses rolled sheets (thin gauge) or pre-cut stacked sheets (thick or heavy gauge). Thin gauge material is dominant in the disposable packaging sector, especially in the retail markets. Heavy or thick gauge material is commonly used as permanent components in such things as refrigerators, automobiles and spas to name a few. PVC is the most commonly used material in any thermoforming production.
All VisiPak thermoforming is manufactured in the USA.
Thermoformed Thin Gauge Packaging
Visipak manufactures a wide variety of thermoformed packaging solutions that are ideal for nearly any product line. Popular options include clear plastic clamshells, blister packaging, and thermoformed trays and inserts.
Heavy Gauge Thermoforming
While manufacturing thick gauge thermoforming trays has been a focus for us, our capabilities extend beyond, and our engineers will assist in designing and providing efficient and effective thermoforming solutions for your project.
Thin Gauge Thermoforming
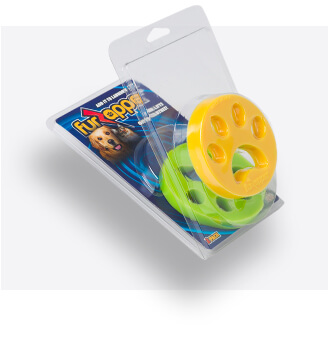
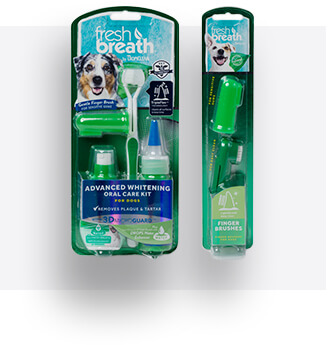
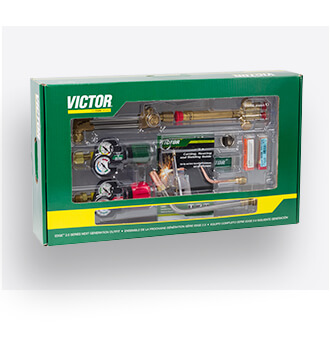
Heavy Gauge Thermoforming
Engineering and Prototypes
Outside of an extensive line of stock clamshells, most thermoformed items are custom designed to fit the intended contents. Our custom thermoforming design experience over multiple years has given us an advantage and we closely advise clients of the best options for their applications. Using cutting-edge manufacturing techniques, our engineers will advise on material, process, and design to ensure the outcome is the most economical and efficient custom thermoforming product.
Design
Not only do we have over 50 years of design experience, but we utilize some of the most sophisticated design and manufacturing software. We’ve grown in CAD CAM technology beginning in the early years of AutoCAD, then Pro-Engineer software.
Tooling
Collaborating with all our locations, we work seamlessly using PTC Creo and Siemens NX programs to seamlessly integrate the tooling fabrication process.
The Equipment
Our thin gauge, in-line thermoforming machines produce high volume quality parts from a variety of materials. The material moves through the heating section into the forming section where pressure and/or vacuum forces the material onto the mold. The process continues to the next station where the forms are die-cut.
Generally, vacuum forming refers to all sheet forming methods. Pressure aids vacuum forming to push the material into the mold. The added pressure of this process provides greater detail and textured surfaces in the end product. Creating sharp corners is possible with pressure added during the forming process.
The Equipment
Our thin gauge, in-line thermoforming machines produce high volume quality parts from a variety of materials. The material moves through the heating section into the forming section where pressure and/or vacuum forces the material onto the mold. The process continues to the next station where the forms are die-cut.
Generally, vacuum forming refers to all sheet forming methods. Pressure aids vacuum forming to push the material into the mold. The added pressure of this process provides greater detail and textured surfaces in the end product. Creating sharp corners is possible with pressure added during the forming process.
Benefits of Thermoforming
- Cost Effective Customization
- Quick Turnaround Time
- Inexpensive Molds
- In-house design support and CAD modeling
- In-house tooling and mold fabrication
- In-house thermoforming and CNC trimming